Environmental Health & Safety from the Director's Desk
|
|
|
Lately, we have seen many exciting changes across our University—and for Environmental Health & Safety (EHS), we have three exciting new additions to our team!
First, we have added a Chemical Hygiene Officer (CHO) position. With this new capability, EHS is offering additional laboratory safety support, including, but not limited to, expanded assistance in evaluation and handling of chemicals, creating and revising chemical inventories, and making corrective actions in the laboratory. You will find our new CHO, Adrian Hernandez Ferrer, on our EHS website's contact page—you may have already met him in your laboratory or building. He is excited to join our team and help further your research needs.
Our new Safety Manager for Hazardous Materials is Brian Cumbie. He is already making an impact throughout the University, bringing a wealth of regulatory knowledge with him to the position. To learn more about Brian, see our Hazardous Waste news section below.
With the departure of our biosafety team member, Marlena Drane, we have filled her position with Quintin James, who you will have the opportunity to meet as he passes through the laboratories during this summer's inspection period.
Remember, if you see or smell anything unusual, report any concerns by calling, emailing, or clicking our "Report Safety Concerns" button on the EHS website.
As always, we hope you find the information in this newsletter informative and useful, and we look forward to continuing to assist you in a safe and productive manner.
Warm regards,
Jennifer Laine, DrPH Executive Director, EHS
|
|
|
A Tale of Two Laboratory Fires
In October and November 2022, two laboratory fires occurred at our Coral Gables and Medical campuses respectively, which resulted in some damage to the labs and equipment; but thankfully, no injuries!
Fire 1
On October 2, 2022, a fire broke out in a research laboratory at the Coral Gables campus where chemicals inside a fume hood cabinet appeared to spontaneously combust resulting in damage both inside and outside of the cabinet and hood. Two key factors in containing and extinguishing the fire were the activation of the nearby fire sprinkler head and the quick response by the Coral Gables Fire Department. The building was evacuated without incident. The fume hood was damaged beyond repair and removed from the laboratory. Note: this fire happened on a Sunday! Chemicals will react under the right conditions, even if no one is present in the laboratory. Helpful methods of avoiding adverse events are to ensure (a) your chemicals are properly stored and segregated, and (b) chemicals that are expired or have damaged containers are sent for disposal.
|
|
|
|
Lessons Learned
- Keep the fume hoods and storage cabinet free of clutter.
- Store incompatible chemicals in separate areas.
- Dispose of old chemicals and chemicals with damaged containers.
- Fire alarms and sprinkler systems activated, extinguishing the fire.
- The Fire Department arrived quickly and could easily access the building and laboratory.
- The fire was wholly contained within the fume hood cabinet.
- Excellent cooperation from the researcher, his team and the Department of Chemistry greatly aided in the overall emergency response to the event.
Fire 2
A spontaneous fire is believed to have occurred sometime between October 31 and November 2, 2022, in a research laboratory at the Medical campus inside the fume hood cabinet. The damage was discovered by the Dermatology staff on November 2, when the team noticed soot around the cabinet doors. The fume hood was damaged beyond repair and removed from the building. Upon inspection, an old piece of equipment was found inside of the cabinet. While it appeared to not have been in recent use, it had remained connected to power, and was likely the source of this fire event. To avoid this occurring in your laboratory, please take a few moments to look around and ensure that there are no pieces of equipment in disrepair and that equipment is turned off when not in use.
|
|
|
|
Lessons Learned
- Unplug old or damaged equipment. Dispose of any surplus. Do not hold onto equipment that was inherited with the space or is not recognizable as belonging to a researcher and is not being properly maintained.
- Turn equipment off when not in use.
- This room is not equipped with either a smoke detector or sprinklers.
- The fire was wholly contained within the safety cabinet.
Key Take-Away
Proper laboratory safety training, adherence to standard operating procedures (SOPs), and good housekeeping are the three key factors in preventing laboratory fires.
|
|
|
|
We are pleased to introduce our new Hazardous Materials (Hazmat) Manager, Brian Cumbie who joined the team on May 22, 2023.
The Hazmat Manager serves to maintain the University's compliance with Federal, State, and Local environmental regulations. Brian joins our team with over seven years of experience with the Florida Department of Environmental Protection serving the residents of Florida. His experience includes water quality analysis, solid and hazardous regulation, air regulation, and emergency response. He also served as a branch office manager for the Department overseeing multiple regulatory and permitting programs.
As Hazmat Manager, Brian oversees a team of Hazardous Materials Safety Specialists who collect and manage hazardous wastes for the University. He is also responsible for maintaining the University's Hazardous Waste reporting, Industrial Wastewater permits, Air permits, and Petroleum Storage Tank registrations.
Brian's main objectives are to provide a safe environment for our University community by minimizing our exposure to hazardous wastes while maintaining the University's excellent compliance with the programs under his purview. For any questions regarding the management of hazardous wastes, please contact Brian Cumbie at bxc933@miami.edu.
|
|
|
Lab Inspection Deficiencies and Corrective Actions
Every year EHS updates the annual lab inspection to include a new item or two that we see as common deficiencies across the campuses. Last year that included the roll out of the new chemical inventory template required for chemical inventory submissions. This year we are asking laboratories to update their contact information in BioRAFT (now ShiShield) to ensure we have a phone number we can reach 24/7 in the event of an emergency. This is key in case of incidents such as the above referenced fires. Being able to reach the laboratory personnel make a huge difference in the effectiveness of emergency response. The updated checklist is provided annually and sent out as we schedule inspections, in addition to being posted on our website for those who would like to review it on demand.
The biggest change this year, however, is not on the annual checklist. For the 2023 inspection cycle, there is a new corrective action enforcement policy. This new policy requires labs to address deficiencies found during lab inspections in a timely manner. Corrective actions should be implemented as soon as possible, but labs will be given four weeks after receiving their inspections reports to roll out corrective actions to address found deficiencies. If corrective actions cannot be implemented within that period, the lab must contact our office to detail what progress is being made and establish a timeline for implementation. Otherwise, EHS will notify the noncompliance to the department chair, the Vice Provost of Research, the EHS Executive Director, the Institutional Animal Care and Use Committee (IACUC), and Institutional Biosafety Committee (IBC). Further, this new policy will apply retroactively, requiring labs to correct any deficiencies found in previous lab inspections after receiving their current 2023 inspection report.
The new policy was written not to be punitive, but to establish a framework and expectation that deficiencies found during inspections shall be corrected in a reasonable time. If your deficiency cannot be easily corrected or might require a longer timeline to complete, keep an open line of communication with EHS and request assistance, if needed. Additionally, we recommend coordinating a time for your lab inspection when you can be present to conduct annual inspections. Being present during the inspection can ensure your awareness and understanding of deficiencies before you even receive the report. This gives you an opportunity to brainstorm solutions with EHS, maybe even correcting deficiencies onsite, and provides extra time for the lab to work on corrections.
As always, safety is very much a collaborative effort, so do not hesitate to reach out to us if you have questions.
|
|
|
Respiratory Protection in the Workplace
Many, if not all physical as well as chemical contaminants find their way into the body through the respiratory system. This fact may cause some to assume a respirator is the best way to prevent exposure, however, that may not be the case.
A respirator is just one of many safety devices found in the workplace. There are many types of respirators that offer various levels of protection; however, they all fall into a general category called personal protective equipment (or PPE).
Just as a physician is careful in prescribing the right medication to the patient, safety professionals must exercise just as much care. The wrong type of PPE may not reduce exposure to the desired level or may prove not to be effective, creating a false sense of security, or worse.
The National Institute of Occupational Safety and Health (NIOSH) has ranked, in terms of effectiveness, the various ways in which employers can make sure their workers are protected. This inverted pyramid is known as the NIOSH Hierarchy of Controls (shown below).
|
|
|
|
In its Respiratory Protection Standard, the Occupational Safety and Health Administration requires that the employer, whenever possible, protects the worker through a more effective way (engineering controls) rather than the lowest (PPE).
In the control of those occupational diseases caused by breathing air contaminated with harmful dusts, fogs, fumes, mists, gases, smokes, sprays, or vapors, the primary objective shall be to prevent atmospheric contamination. This shall be accomplished as far as feasible by accepted engineering control measures (for example, enclosure or confinement of the operation, general and local ventilation, and substitution of less toxic materials). When effective engineering controls are not feasible, or while they are being instituted, appropriate respirators shall be used pursuant to this section. (Emphasis added). 29 CFR 1910.134(a)(1)
Prior to prescribing the use of a respirator, an assessment should be conducted to ensure that these other methods of exposure prevention have been considered.
If you do need to use a respirator, you should be in a University Respiratory Protection Program, have the correct brand and fit for your facial features, be trained on the use of the respirator, and have passed the medical questionnaire. Continued use of a respirator requires an annual fit test.
At EHS, we have dedicated professionals who specialize in this area and are ready to answer any questions you may have or assist you in being safe and in compliance.
|
|
|
|
State-of-the-art Quantitative Fit Testing such as that used at UM (Source: tsi.com)
|
|
|
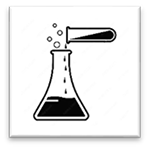
We are pleased to introduce our new Chemical Hygiene Officer (CHO), Adrian Hernandez Ferrer who joined the EHS team on April 3, 2023. The CHO serves to enforce chemical safety standards and protect the University community from exposures and accidents involving chemicals and their hazards. Adrian is a Chemical Engineer and Certified Safety Professional with 18 years' experience in the pharmaceutical, manufacturing, transport safety and chemical safety fields. He was also a volunteer firefighter at the Universidad Central de Venezuela for 17 years.
As the CHO, Adrian is responsible for facilitating and implementing the Chemical Hygiene Plan (CHP) - a written program outlining the policies, procedures and responsibilities that protect the University community from health hazards associated with the use of hazardous chemicals.
He is also responsible for assisting in maintaining and updating the Chemical Inventories across the University. By keeping the Chemical Inventory current, Adrian will be able to identify any potentially toxic or harmful substances and recommend safer alternatives where possible to prevent accidents and injuries. You can download our Chemical Inventory template here.
2023 is an important chemical safety year in terms of updating and managing the chemical inventories. For assistance in developing good chemical inventory management, please contact Adrian at arh38@med.miami.edu.
|
|
|
|